
Unleashing the Power of Private Label Wipes: Your Ultimate Guide
March 15, 2024
Are Bamboo Wipes Truly Biodegradable
March 27, 2024Embark on a fascinating journey through the intricate world of wet wipe production from inception to the final product. Have you ever stopped to ponder the meticulous process behind the convenience of a single wet wipe? It's more than just a simple sheet moistened with a cleansing solution; it's a testament to precision and innovation. As we delve into the behind-the-scenes of how wet wipes are manufactured, prepare to be astounded by the blend of art and science that goes into creating these everyday essentials. Behind every convenient wipe lies a series of carefully orchestrated steps that seamlessly come together like a well-choreographed dance. From the selection of raw materials to the cutting-edge technologies employed in manufacturing, each stage plays a pivotal role in ensuring that every wipe meets stringent quality standards. So, buckle up as we unravel the mysteries behind the production lines and unveil the secrets of how are wet wipes manufactured with a level of detail that will leave you marveling at the sheer ingenuity behind these seemingly humble products.
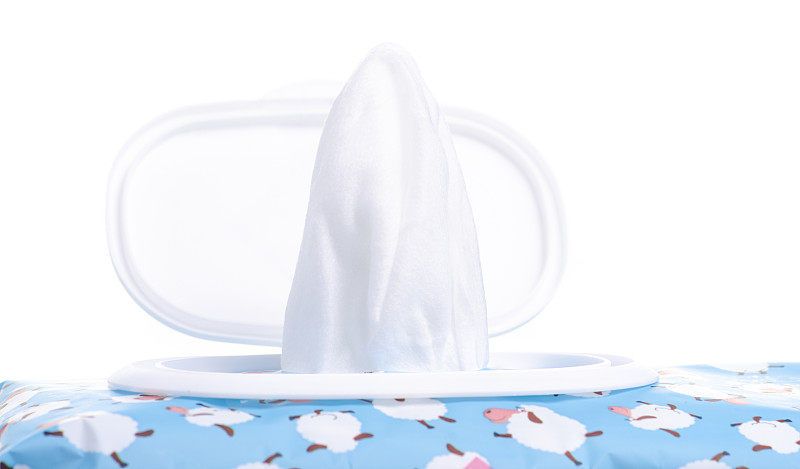
Raw Materials Selection: The Foundation of Wet Wipe Production
The journey of wet wipe manufacturing begins with the careful selection of raw materials. Every component is chosen with precision to ensure the final product meets the highest quality standards. The main ingredients in wet wipes are water, cleansing agents, and fabric. Let's take a closer look at each element:
Water: The primary ingredient in wet wipes is water, which serves as the base for the cleansing solution. Purified water is typically used to ensure that no impurities or contaminants are present.
Cleansing Agents: Various cleansing agents are added to the water to create an effective solution for cleaning and disinfecting. These agents can include surfactants, preservatives, and antimicrobial compounds. The specific formulation depends on the intended use of the wet wipes.
Fabric: The fabric used in wet wipes is typically a non-woven material made from fibers such as polyester, viscose, or cotton. Non-woven fabrics are chosen for their softness, absorbency, and durability. They also allow for easy dispensing and folding during production.
Once these raw materials have been carefully selected, they are brought together in a controlled environment to create the perfect blend of moisture and cleansing solution.
Formulation: Crafting the Perfect Cleansing Solution
The formulation of the cleansing solution is a crucial step in wet wipe production. It involves combining water with various cleansing agents to create a solution that effectively cleanses and disinfects while remaining gentle on the skin.
The specific formulation depends on factors such as the intended use of the wet wipes (e.g., baby wipes, makeup remover wipes) and any specific requirements or regulations that need to be met (e.g., hypoallergenic formulas). Manufacturers carefully balance different ingredients to achieve the desired cleansing properties, pH level, and fragrance.
Formulation is a delicate process that requires expertise and extensive testing. Manufacturers conduct thorough research and development to ensure that the cleansing solution is safe, effective, and pleasant to use.
Non-Woven Fabric Manufacturing: The Key to Wipe Texture and Strength
The texture and strength of wet wipes are largely determined by the non-woven fabric used in their production. Non-woven fabrics are created by bonding fibers together using heat, chemicals, or mechanical processes.
The manufacturing process begins with the preparation of the fibers. These fibers can be natural (e.g., cotton) or synthetic (e.g., polyester). They are cleaned, carded, and sometimes spun into yarn before being transformed into a web-like structure.
Once the web of fibers is formed, it undergoes a bonding process to give it strength and stability. This can be achieved through methods such as thermal bonding (using heat), chemical bonding (using adhesives), or mechanical bonding (using needles or water jets).
The choice of bonding method depends on factors such as the desired texture, strength, and absorbency of the final product. Manufacturers carefully select the appropriate non-woven fabric manufacturing technique to ensure that each wipe meets their specific requirements.
Moistening Process: Infusing Wipes with the Ideal Moisture Content
The moistening process is where dry wipes are transformed into their familiar wet form. It involves saturating the non-woven fabric with the cleansing solution to achieve the ideal moisture content.
This process requires precision to ensure that each wipe is evenly moistened without becoming too dry or overly saturated. Manufacturers use specialized machinery that controls the amount of solution applied to each wipe.
During this stage, quality control measures are implemented to ensure that the moisture content meets the desired specifications. Wipes that do not meet the required moisture level are rejected to maintain consistency and effectiveness.
Cutting and Folding: Precision Engineering for Uniform Wipe Size
Once the non-woven fabric has been moistened, it is time to transform it into individual wipes of uniform size. This is achieved through cutting and folding processes that require precision engineering.
Specialized machinery is used to cut the large sheets of fabric into smaller, standardized sizes. The cutting process ensures that each wipe is consistent in dimensions, allowing for easy dispensing and use.
After cutting, the wipes are folded into their familiar shape. Folding machines carefully fold each wipe to create a neat and compact product that is easy to handle and store.
Packaging and Sealing: Safeguarding Freshness and Hygiene
The packaging stage plays a crucial role in preserving the freshness, hygiene, and convenience of wet wipes. It involves enclosing the individual wipes in airtight packaging materials that protect them from contamination.
Manufacturers use various packaging formats such as resealable packs or single-use sachets. These packages are designed to be user-friendly, ensuring easy access to each wipe while keeping the remaining ones sealed for future use.
During this stage, quality control checks are conducted to ensure that each package contains the correct number of wipes and that they are properly sealed. This helps maintain product integrity throughout its shelf life.
Quality Control: Rigorous Testing to Ensure Excellence
Throughout every stage of wet wipe production, rigorous quality control measures are implemented to ensure excellence in every aspect of manufacturing. Manufacturers conduct various tests and inspections to verify that each wipe meets their stringent standards.
Quality control checks may include testing the moisture content, pH level, strength, and absorbency of the wipes. Additionally, microbial testing is often performed to ensure that the wipes are free from harmful bacteria or contaminants.
Any wipes that do not meet the required specifications are rejected to maintain consistency and uphold the highest quality standards. This commitment to quality control ensures that consumers can trust in the effectiveness and safety of wet wipes.
Automation and Innovation: Streamlining Production for Efficiency
The manufacturing process of wet wipes has evolved significantly over time, thanks to automation and innovation. Manufacturers have embraced cutting-edge technologies to streamline production and improve efficiency.
Automated machinery is used for various stages of production, including formulation, non-woven fabric manufacturing, moistening, cutting, folding, and packaging. These machines ensure consistent results while reducing human error and increasing productivity.
Innovation also plays a crucial role in wet wipe manufacturing. Manufacturers continuously explore new materials, formulations, and packaging solutions to enhance the performance and sustainability of their products.
Sustainability Efforts: Environmentally Conscious Manufacturing Practices
In recent years, there has been a growing focus on sustainability in wet wipe manufacturing. Manufacturers are adopting environmentally conscious practices throughout the production process.
This includes using sustainable raw materials such as biodegradable or compostable non-woven fabrics. Additionally, efforts are made to reduce water consumption during formulation and moistening processes.
Packaging materials are also being optimized for recyclability or made from recycled materials whenever possible. Manufacturers strive to minimize waste generation by implementing efficient production techniques.
Conclusion: The Intricate Tapestry of Wet Wipe Manufacturing
The journey from raw materials selection to the final product is a testament to the intricate tapestry of wet wipe manufacturing. Each stage of the process, from formulation to packaging, is carefully orchestrated to create a product that meets the highest quality standards.
Through innovation, automation, and sustainability efforts, manufacturers continue to refine and improve the production of wet wipes. The result is a convenient and effective product that enhances our daily lives in countless ways.
Next time you reach for a wet wipe, take a moment to appreciate the craftsmanship and expertise that goes into its creation. Behind every wipe lies a world of precision engineering and scientific innovation.